Platform
The Rossini Platform
The Rossini Platform is an aggregation of Core and Extra components as a set of interconnected elements, represented as an integrated set of layers, each related to a specific dimension/function.
Hardware and/or Software Components:
CORE components to build a Rossini Platform
EXTRA components, useful for a given application scenario
Core and Extra
Components
The Platform Components
Learn more about the respective Components by watching the demonstration videos.
1.
RS⁴ Controller, Vision and Laser
The RS⁴ Controller, with its I/O interfaces supports multiple devices, data fusion and elaboration capabilities
Watch Video
2.
Radar, Skin and Safe Position Signalling
The RS⁴ Controller, with its I/O interfaces supporting multiple devices, data fusion and elaboration capabilities
Watch video
3.Semantic Scene Map
Through the employment of artificial intelligence techniques, a Semantic Scene Map integrating geometric and semantic information will be generated, which will in turn create a set of virtual “Dynamic Shells” for safety, surrounding each object in the scene.
Watch the video
4.Cognitive & Flexible Execution Layer and Orchestrator

The Cognitive Layer will be provided by a high-level scheduler, capable of dynamically planning a set of cooperative actions that the robot needs to execute, and to update them when the working environment conditions, captured by the Semantic Scene Map, change.
Watch the video
5.
Evaluation of Hazard Potential in Free Collisions

It will interpret the high-level action to execute and will generate the most efficient and safety preserving low-level plan for the robot, thus optimizing trade-off between safety and productivity in the workcell.
Watch the video
6.
The Human Factor in HR Collaboration

The Human Layer will ensure the inclusion of human-related factors from the early design phases of collaborative applications design, and the constant monitoring of factors influencing job quality during robotic operations.
Watch the video
7.
The Rossini Collaborative Robot

It will encompass a novel concept of manipulators with built-in safety features, capable of reducing the separation distance between the man and the operator when performing collaborative applications, thus increasing the degree of freedom for robotic applications design.
Watch the video
8.
Virtual Design Tool

It will provide integrators with a set of tools and guidelines to ensure inherent safety in design of HRC applications, and to speed up application configuration and reconfiguration.
Watch the video
Use Cases
We are testing in real industrial environments
The Rossini Platform will be demonstrated into 3 industrial environments up to TRL6. The use cases have been chosen trying to have the widest possible span in terms of application sector, tasks to be executed technologies to be deployed.

Use Case 1
Domestic Appliances Assembly
In the WHIRLPOOL use case, ROSSINI will deploy the adaptive features of the Human Layer and the Safety Aware Control Architecture in a highly challenging context (continuous flow line) in terms of working speed. The manipulator will be chosen among commercial products, to demonstrate the platform potential to interact with and be wrapped around third party technologies.
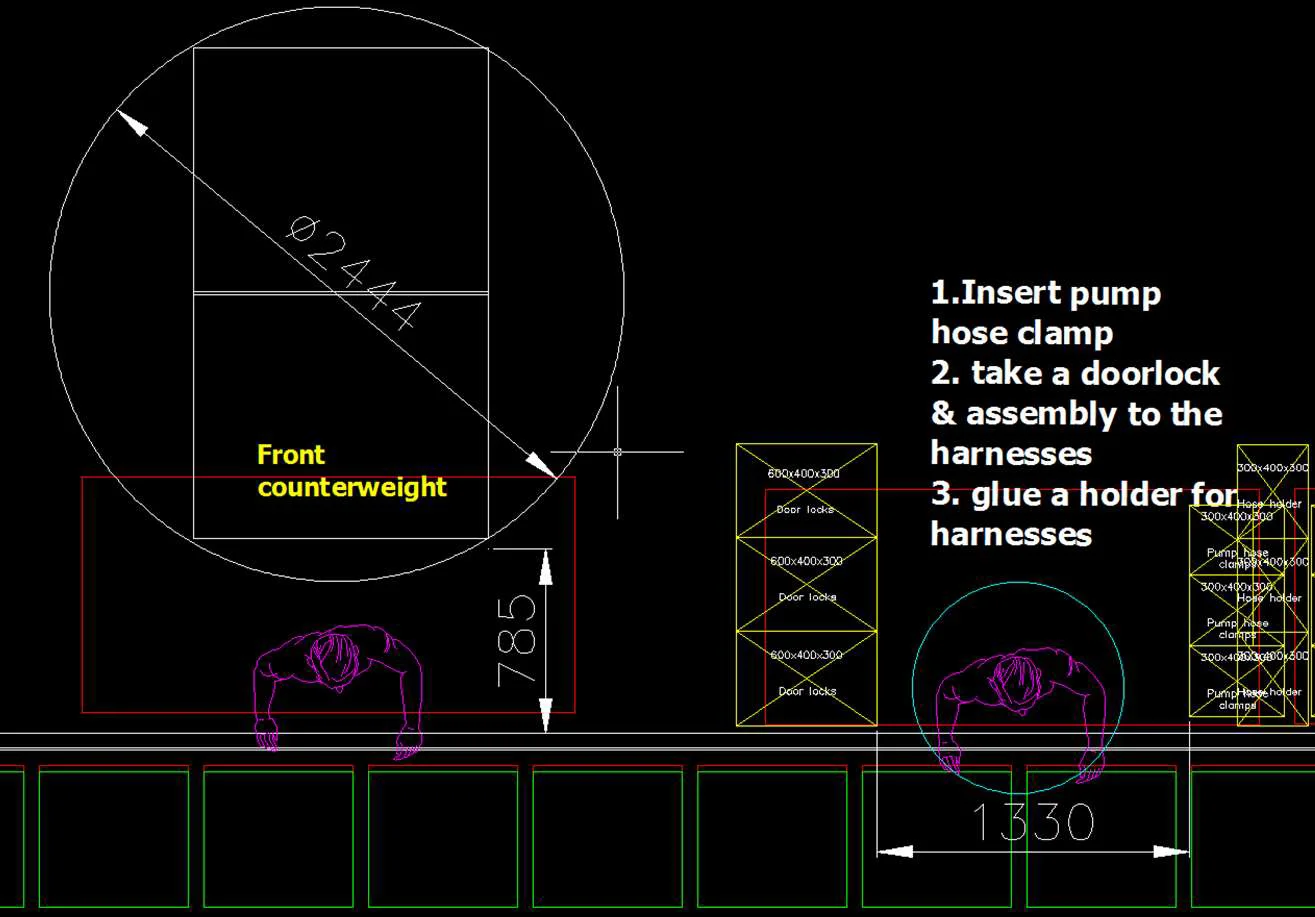
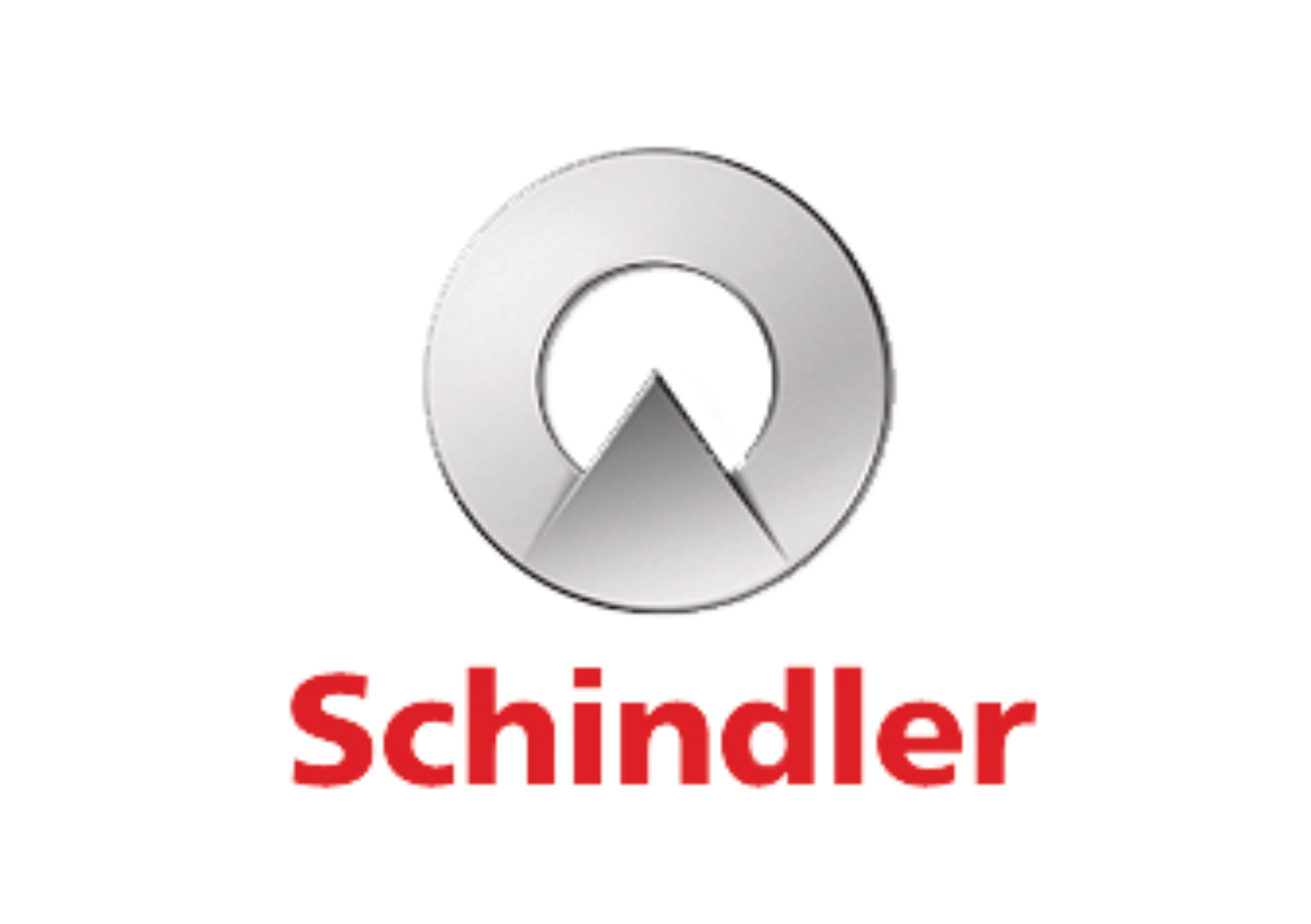
Use Case 2
Electronic Components Production
In the SCHINDLER use case, ROSSINI will demonstrate the features of the Collaborative by Birth Robotic Manipulator, delivering a low payload robotic arm for electronic components production, integrated with the other platform components (sensing system, controller, etc.). Given the user’s high production variability, the promised ROSSINI performance in terms of production reconfiguration cost savings will be tested.
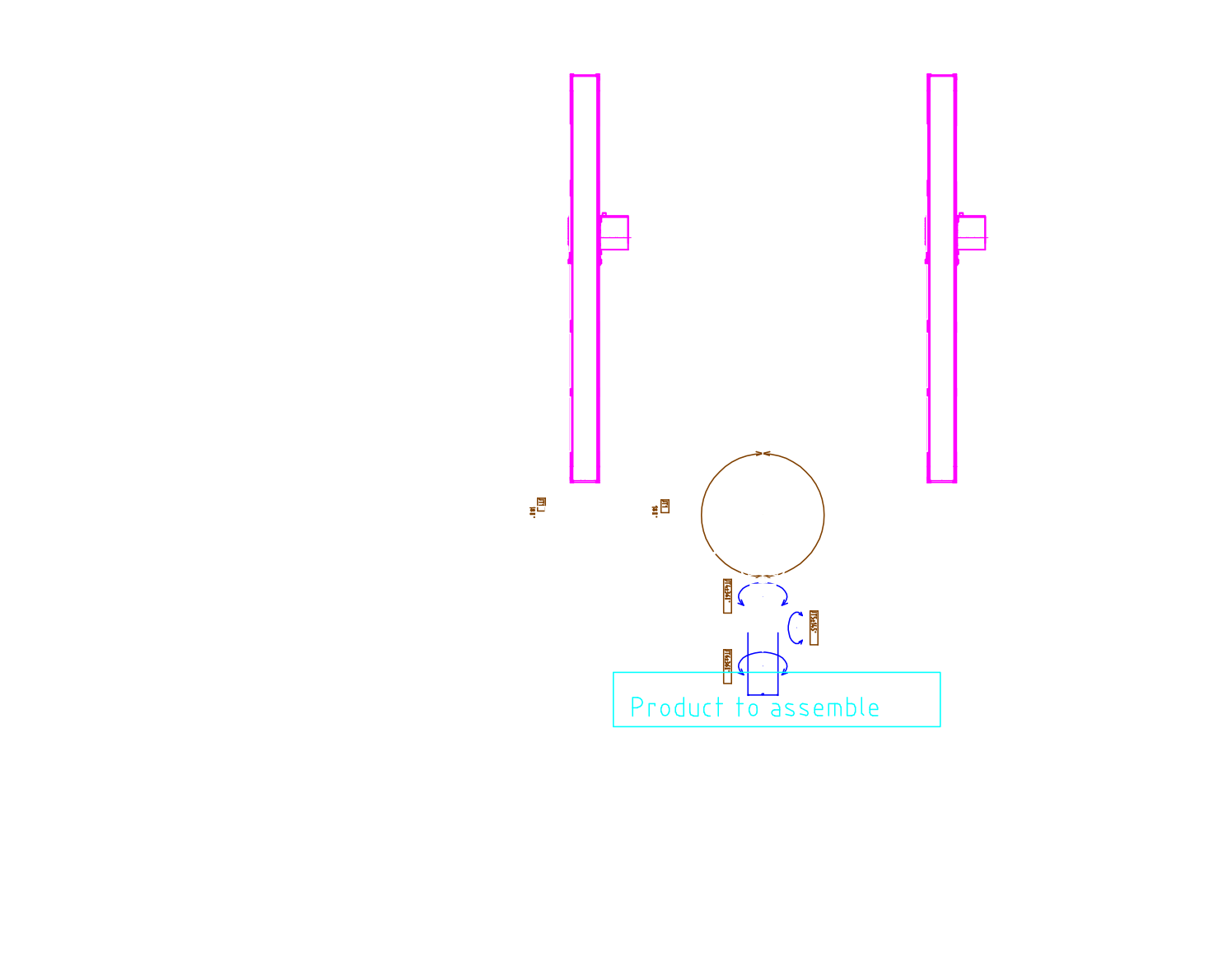

Use Case 3
Food Products Packaging
In the IMA use case, ROSSINI will deploy a medium payload manipulator mounted on an AGV (mobile robotic platform). The Human Layer and the Control Architecture will be confronted with the challenge to manage navigation operations as well as other operations. Being IMA also a robot integrator, the demonstrator will be easily replicated.
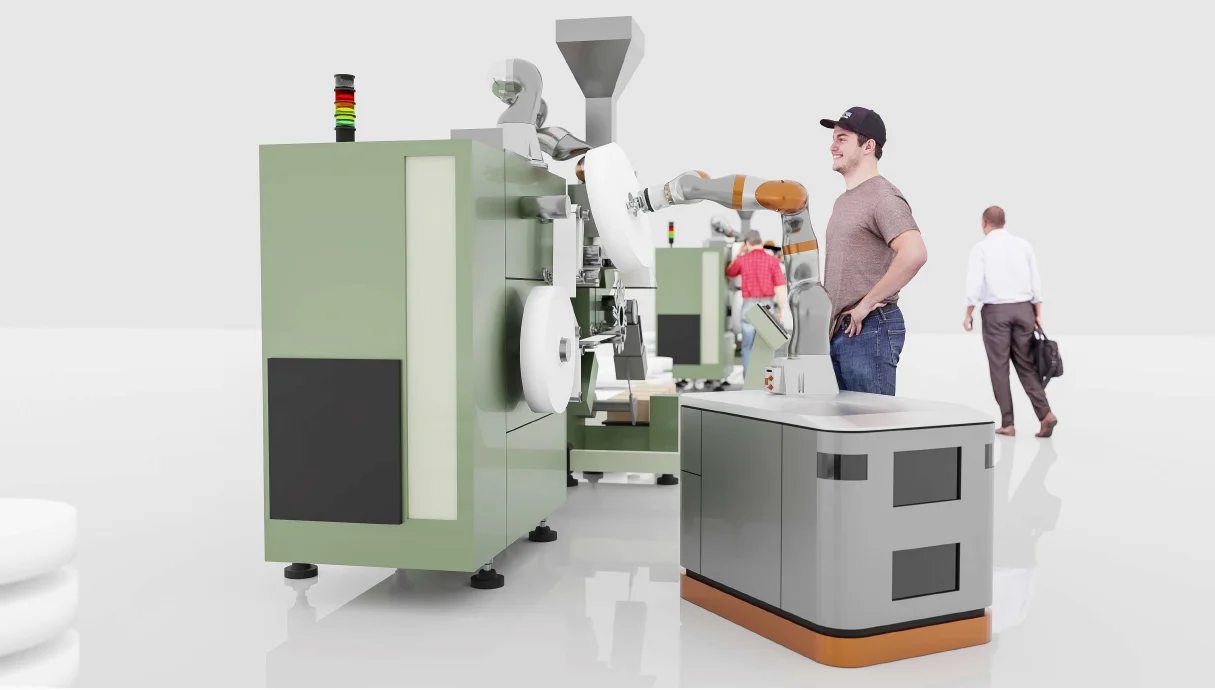